04-010-10 Inventory Control - Physical Inventory Process
Overview
In this document, we will examine the Physical Inventory Process. Inventory issues, receipts, and cycle counts can be performed from within the wireless module. This streamlined process allows the user to adjust inventory in a very efficient process.
The cycle count is based upon a three-step management process:
1. Management creates a job that defines the area of inventory to be counted.
2. The user selects the job and then scans and counts the items within the designated area.
3. Management reviews the count within the system, adjusting postings as required, and then posts the job to the system.
Upon completing the cycle count, the system will report items missed during the cycle count for a specific location, allowing for additional edits to occur as required. The system automatically adjusts the non-scanned items on-hand to zero and marks items as non-sellable based upon directives.
Create Physical Groups
Physical Groups allow a method of organization strongly related to the physical location codes assigned within the store. Physical Groups are created within the Wireless Inventory module with the following process.
1. Options > Wireless Menu
2. Select Physical Item Maintenance
3. Select New
4. In this example four Physical Groups have been created to cycle count four sections of Diablo parts.
Create Location Labels
During the physical cycle count process, the system will allow the user to assign a Location without any additional steps. Take advantage of this process by creating a Location Label for each 4 foot display.
1. Select IC > Reports > Location Label
2.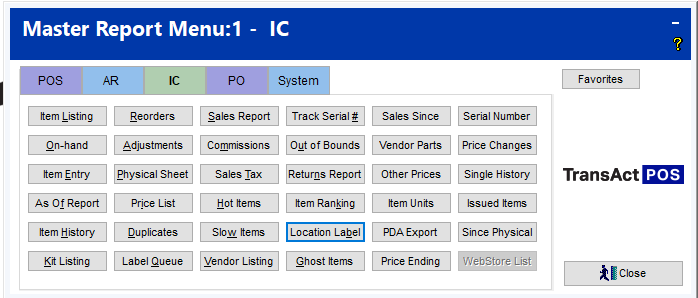
3. Enter the Location ID to be applied to the section of inventory being counted. Typically, entering just the Location ID is enough information. The Description field may be filled in, but not required.
4. Apply the Location ID Label in a consistent manner within displays.